本田正在通往電動化的路上奮力追逐。
3月4日,蓋世汽車獲悉,本田首次公開了以鋁材實現車身零部件一體成型的大型生產設備。
據悉,這種設備可使車身零部件數量減少至十分之一以下,有助于降低純(EV)成本。本田首先將為2026年上市的新款EV引入該技術。
對比來看,美國特斯拉和中國車企以及汽車產業相關企業已率先引入零部件一體成型技術。
可見,本田正在加緊扭轉局面。
蓋世汽車認為,在全球電動汽車產業的激烈角逐中,技術創新成為企業脫穎而出、搶占市場份額的關鍵。本田引入車身零部件一體成型設備這一舉措,正揭示出日系傳統汽車制造領域的新變革,以及本田在這場電動化競賽中奮力追趕中美企業的決心。
提效率,卷成本
本田首次公開的鋁材車身零部件一體成型大型生產設備,是邁向電動汽車制造成本優化的一大步。
在傳統汽車制造中,車身往往由大量零部件組裝而成,工序繁瑣、耗時費力,且需要眾多的模具與人工操作。
據悉一臺普通轎車的車身,需要組裝多達數百乃至上千個零部件,從車身框架的主體結構件,到車門、引擎蓋、后備箱蓋等大型覆蓋件,再到各類用于連接、支撐的小型部件,林林總總,數量繁多。這些零部件形態各異,尺寸精度要求極高,每個都在車身整體架構中承擔著獨特的功能。
首先是零部件的沖壓環節,不同形狀和規格的金屬板材需被送入大型沖壓機,在巨大壓力下被精準沖壓成型。光是沖壓工序,針對不同零部件就可能需要數十套甚至上百套專用模具,每一套模具的設計、制造與調試都需耗費大量時間與高昂成本。
沖壓完成后,零部件進入焊接車間,這里堪稱是 “鋼鐵叢林”,人工操作與自動化焊接設備并存。工人需憑借精湛技藝,將一個個沖壓好的零部件按照嚴格的設計圖紙,通過點焊、弧焊等多種焊接方式,精確無誤地拼接在一起。在焊接過程中,既要確保焊點牢固,滿足車身強度要求,又要嚴格控制焊接變形,以免影響車身整體精度。
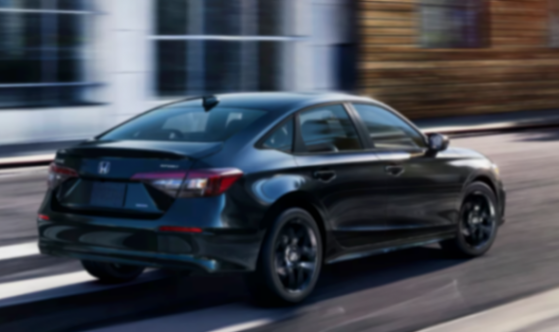
圖源:本田
車身焊接完成后,需進行多道精細的涂裝工藝,以保護車身免受腐蝕,同時賦予車輛美觀的外觀。從底漆、中涂到面漆,每一層涂料的噴涂都需在特定環境下進行,對溫度、濕度、噴涂壓力等參數有著嚴格要求。人工操作時,工人需手持噴槍,均勻地將涂料噴涂在車身表面,確保每一處都能被精準覆蓋,稍有遺漏或噴涂不均,就可能在后續使用中出現漆面問題。整個涂裝過程不僅需要大量人工參與,而且還需配備專業的涂裝設備與環保設施,以確保生產過程符合環保標準。
模具方面,傳統汽車制造對模具的依賴程度極高。如前文所述,沖壓工序中的每一種零部件都需要專屬模具,而且隨著汽車款式更新換代,模具也需相應調整或重新制造。一套高精度的汽車沖壓模具,從設計構思、計算機模擬分析、精密加工制造,到最后的安裝調試,往往需要數月時間,成本高達數百萬甚至上千萬元。
不僅如此,模具在使用過程中還需定期維護與保養,以確保其精度與使用壽命,這無疑進一步增加了生產的復雜性與成本投入。
人工操作貫穿于整個車身制造流程,從零部件的搬運、定位,到焊接、涂裝等關鍵工序,人工的精細操作與豐富經驗起著不可或缺的作用。但人工操作受限于人的體能與注意力,生產效率相對較低,而且不同工人之間的技術水平與操作習慣存在差異,這也給產品質量的一致性帶來了挑戰。
增加定價靈活性
在如今快節奏的汽車市場競爭環境下,傳統汽車制造中車身組裝的這些繁瑣工序、高昂的模具成本以及對人工的高度依賴,正逐漸成為本田在電動汽車領域快速發展的掣肘,亟待通過創新技術進行突破與變革 。
以特斯拉為例,其率先在Model Y車型上采用一體化壓鑄技術,將原本70多個零部件組成的后車身簡化為1-2個大型壓鑄件。這一技術不僅大幅減少了零部件數量,降低了供應鏈管理的復雜度,還縮短了生產周期,提升了生產效率。
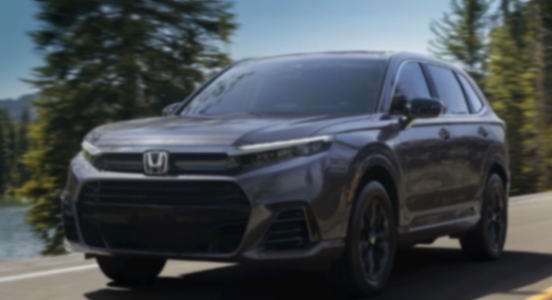
圖源:本田
本田此次引入一體成型技術,目標同樣清晰:將車身零部件數量削減至十分之一以下。零部件的減少意味著組裝時間大幅縮短,人力成本隨之降低;同時,更少的零部件意味著對模具的需求減少,模具開發與維護成本顯著下降。
據估算,僅模具成本方面,一款傳統汽車模具開發費用可能高達數億美元,而一體成型技術可削減至少三分之一的模具開支。
這對于追求成本效益的電動汽車生產而言,無疑是巨大的吸引力。
本田有望通過這一創新實現成本結構的優化,在價格競爭激烈的電動汽車市場中獲得更多定價靈活性。